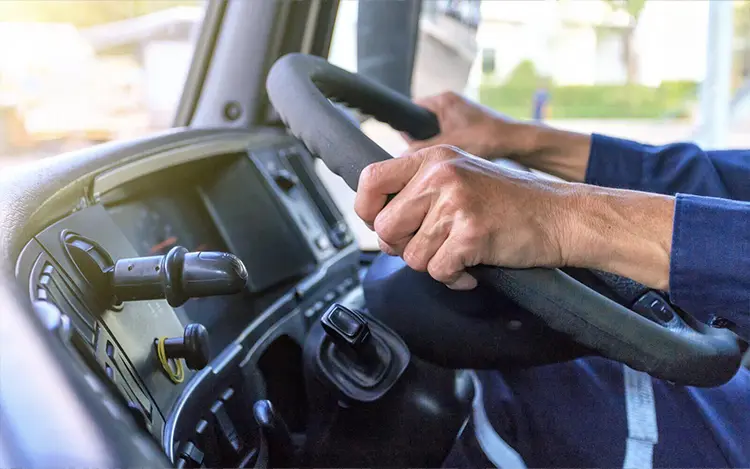
GPSを活用した配車システム
輸送業界の課題を解決するGPS配車システム「スカイワン」
近年輸送業界では、運転手不足、燃料価格の高騰、安全・環境対策のコスト増加、道路混雑、若年労働力不足、繁忙期・閑散期の格差拡大、積載率・稼働率の向上、ジャストインタイム輸送、納品先へのサービス向上、品質確保、誤納対策等の課題が山積しており、配車・輸送の合理化・効率化を目指したシステム化の要請が高まっています。
当社はこれらの課題解決に向けて、GPS(Global Positioning System)を活用した配車管理システムを主に生コン業界に提供しており、本システムは全国の生コン会社・輸送会社、生コンクリート協同組合の共同配車事業等に採用されてきました。
ここではGPSを活用した配車システムの開発の歴史や、特徴、導入効果等について述べます。
我が国初のGPS配車システム「スカイワン」を開発
当社は前身のシステム綜合開発株式会社の時代、1991年に業務用無線機を通信機器としたGPS運行管理システム「スカイワン」を開発し、郵政省(現総務省)の国内認可第一号を取得しました。
発表時はタクシー業界からの反響が大きく、タクシー向け配車システムとして開発をスタートしました。写真1に当時のスカイワンを示します。

タクシー業界向け開発で得られた知見
タクシー向け開発で得られた知見をまとめると次の通りです。
1.車両の位置・動態がほぼリアルタイムで把握でき導入効果は絶大
当時はAVMシステム(Automatic Vehicle Monitoring System)と呼ばれる運行管理システムが普及していました。
AVMシステムはエリアごとの車両の位置管理を大まかに行いますが、配車ポイントに一番近い空車は正確にはわかりません。
一方、スカイワンでは地図上に一番近い空車が表示されていますので、まさに一目瞭然です。
スカイワン導入前は配車後のタクシー到着まで約15分かかっていましたが、スカイワン導入後は約5分に短縮。画期的なシステムの誕生となりました。
2.究極の配車は“実車配車”
皆さんも経験があると思いますが、急に雨が降ったり、電車が運転見合わせになったりといった時は、タクシーの空車が一気に無くなります。
配車室で画面を見ていると、次々と空車が実車に変わって行きます。それでもタクシーを求める電話が鳴りやみません。
そこでスカイワンでは、空車が1台も無くなった状態では、実車中の車両がどこでお客様を降ろして空車になるかを確認し、配車ポイントに近い車両に対して実車中でも配車するようにしました。
3.無線データ通信のトラフィック最適化問題
業務用無線機によるデータ通信の時代は、音声通話とデータ通信を同一の周波数帯で行うため、音声を優先するとデータの遅延や欠落が発生し、データを優先すると通話に支障をきたすといったトレードオフに常に悩まされていました。
車両台数の規模に応じてトラフィックの最適化を図り対処したものの、根本的な解決までには至りませんでした。
しかし、後述する携帯電話網を利用した通信を採用してからは、信頼性の高いデータ通信と無線機による自由な通話が両立でき、問題を一気に解決することができました。
生コン向けGPS配車システム「スカイワンⅡ」の開発
タクシー業界向けのGPS配車システムを開発したことで、多くのノウハウや経験知を得ることができました。
その後は、2003年頃から携帯電話網を利用して生コン業界向けに開発を開始。商品名はスカイワンの後継ということで、「スカイワンⅡ」としました。
生コン輸送には固有の留意点があります。主な点は以下の通りとなります。
1.輸送時間の制約
生コンクリートは文字通りフレッシュな性質であるため、輸送時間が長くなるほどスランプ値や空気量が低下し、品質面での問題が発生します。
JIS A 5308では、練混ぜ開始から荷卸しまでの時間限度を90分と設けており、この時間を超えないように輸送管理を実施する必要があります。
2.材料分離に注意する
輸送中に生コンクリートの材料分離が発生しないように、生コン車の撹拌機能を適切に使用します。
3.現場の進捗や道路状況を勘案し配車する
大型現場などでは、一般的に連続的なコンクリート打込みが行われており、切れ目なく生コンクリートを納入することが求められています。
従って配車オペレータは、常に現場の進捗や道路状況を把握し、最適なピッチで配車を実行する必要があります。
4.誤納の防止
現場の違いや打込み箇所の違いにより、配合の異なる生コンクリートを輸送するため、ヒューマンエラーによる誤納が発生しないよう、伝票内容を徹底確認し、細心の注意を払って輸送します。
5.洗車および安全運転の励行
環境保全および品質管理の観点から、荷卸し後にはシュートの洗浄を、プラントに戻った際にはドラム内の洗浄を行います。
また輸送時や現場内での走行には常に注意し、事故を起こさないよう安全運転を心がけます。
図1にスカイワンⅡの構成図を示します。

スカイワンⅡの主な特徴
スカイワンⅡの主な特徴は次のとおりです。
- 携帯電話網を利用した通信により、エリアの制約が少なく安定的に運用できます。
- 出荷管理システムとのデータ連係により、自動的に運用できます。
- 見るだけで生コン車の位置・動態情報や現場の進捗状況を把握できます。さらにオプションで渋滞情報を表示できます。
- 誤納防止機能により、安心して生コン出荷が行えます。
- 車載端末は、IP無線機、専用車載端末等、お客様の実情に合った端末を選択できます。
スカイワンⅡの導入効果
生コン専用システムとして開発したスカイワンⅡは、お陰様で全国の生コン工場や生コンクリート協同組合で採用していただきました。
数多く寄せられた“お客様の声”の中から、導入効果の一部をご紹介します。
- 現場の進捗状況や渋滞情報の見える化によって配車ピッチを調整し、無駄のない効率的な配車を実現できました。
- 出荷前日に配車シミュレーションや出荷実績データを基に必要車両台数を算出し、出荷当日はスカイワンⅡによる配車管理を行った結果、システム導入前と比較して、1日1台程度の減車ができました。僅か1台ではありますが、年間の庸車費用に換算すると大きなコスト削減となりました。
- 誤納防止機能や各車両の見える化によって、配車オペレータの安心感を高め、出荷多忙時の煩雑な業務も的確に対応できました。
- IP無線機の導入により、以前の業務用無線機と比較して、不感地帯がほとんどなくなり、雑音や混信もなくなったため、利便性が格段に向上しました。
- 出荷管理システムとの自動連係により、現場からの問い合わせに的確に回答ができ、現場へのサービス向上が図れました。
トータルソリューションシステムへ発展
現在では、さらに他のシステムを連係し、トータルソリューションシステムへと発展させることで、生コン工場の業務全体を効率よく運用できるようになりました。
図2にトータルソリューションシステム、写真2に実際の運用状況を示します。


まとめ
これまで述べてきましたスカイワンⅡは、ICT (Information and Communication Technology)を駆使したツールと言い換えることができます。
ツールである以上、それを使いこなすのは人間です。従ってスカイワンⅡの導入効果は、配車オペレータの不断の努力によって実現していることを申し添えておきます。